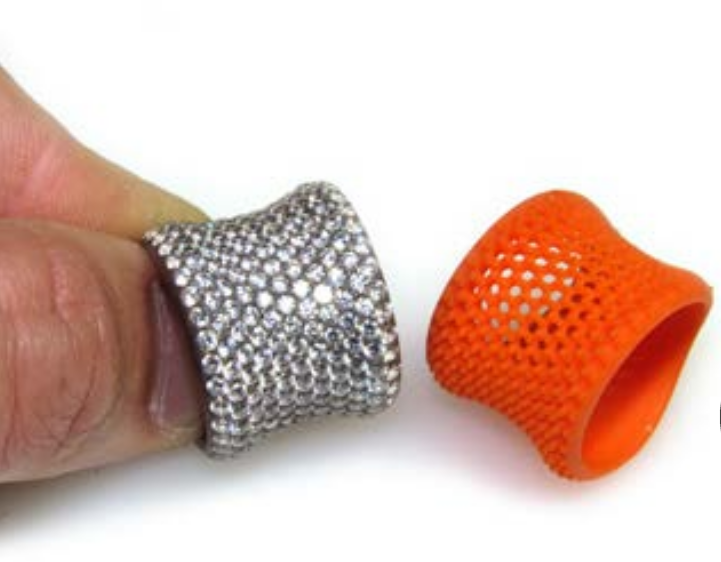
Che rapporti avete con il polo orafo di Valenza?
Essendo nati qui, abbiamo vissuto e respirato il mondo orafo: arriviamo da tre generazioni di gioiellieri e abbiamo lavorato nel settore ricoprendo mansioni diverse. Il mio ingresso nel mondo del 3D, a livello di progettazione, risale al 1995. A quei tempi le cose erano vissute come un segreto industriale, dal momento che il 3D non era alla portata di tutti. La nuova tecnologia si rivelò capace di garantire vantaggi enormi, basti pensare agli orecchini: a noi progettisti, per fare il simmetrico di un oggetto, bastava la pressione di un pulsante. Da allora il 3D si è sviluppato, ha preso piede e con il tempo abbiamo sentito l’esigenza di creare nostri tool per migliorare la progettazione, arrivando a realizzare un software specifico per l’incastonatura. Da lì in poi è nata l’azienda: al software si sono affiancate le macchine, i materiali e da oggi anche la scansione 3D. Abbiamo, insomma, avuto un’evoluzione: a casa nostra eravamo conosciuti come progettisti 3D molto in gamba, tuttavia abbiamo stentato a farci volere bene, non tanto per il software, quanto per i macchinari. I nostri più grandi ammiratori stanno altrove: a Napoli, Roma, Arezzo. A Valenza, invece, confermando che nessuno è profeta in patria, abbiamo notato una certa diffidenza, che stiamo vincendo proprio quest’anno. Le nostre macchine sono sempre più apprezzate, grazie alla serietà e alla qualità della produzione, insieme all’assistenza tecnica, un fattore per noi irrinunciabile.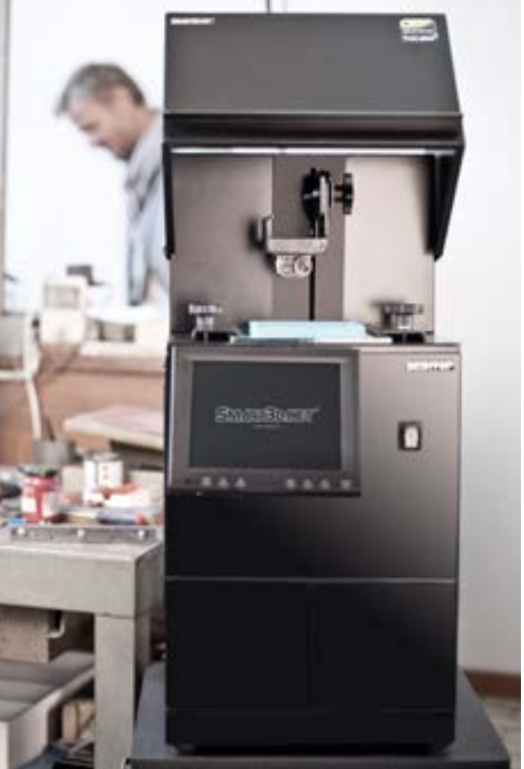
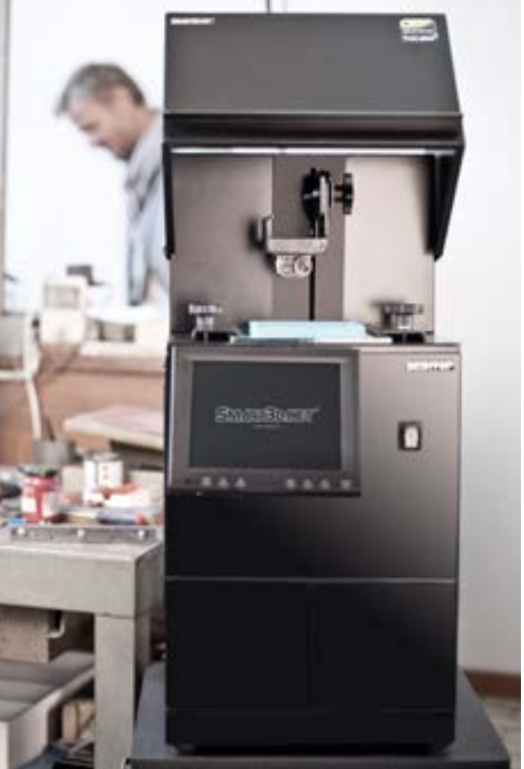
Come si è fatta largo la stampa 3D nel settore orafo?
La stampa 3D è stata accolta bene: fu la progettazione 3D a non essere stata accolta affatto. Ricordo ancora, prima del 2000, che passavo buona parte del mio tempo a
evangelizzare le aziende, a spiegare che il 3D e la progettazione fatta in questa maniera al computer non erano peccato e, di conseguenza, non lo era neppure la stampa. Per quest’ultima, a quei tempi venivano usate macchine lente nel fare degli oggetti: per realizzare un anello impiegavano fino a 12, 24 ore. Inizialmente, si utilizzavano anche le macchine a controllo numerico, poi sono comparsi i primi service di prototipazione; le tecnologie sono andate avanti, oltre alle macchine a getto sono arrivate le stereolitografie, con costi ancora esagerati. Oggi, invece, a Valenza è indispensabile avere un progettista Cad ed è utile avere una stampante internamente. Un’azienda ricerca la stampante 3D per tre motivi fondamentali: per difendere la proprietà intellettuale realizzando un oggetto senza mostrarlo all’esterno; per l’immediatezza del prototipo; per l’economicità del processo. L’oreficeria in questo momento si sta rivolgendo a noi per avere macchine affidabili, che garantiscano un funzionamento continuo e che riescano a fare anche i più piccoli particolari in maniera perfetta. La richiesta di precisione e accuratezza è sensibilmente aumentata.
Il vostro cliente è evoluto nel tempo?
Seguiamo altri settori oltre quello della gioielleria, ma devo dire che è proprio quest’ultimo il più attento alle tecnologie 3D. Mentre una volta bisognava spiegare funzionamento, limiti e vantaggi, oggi, soprattutto nelle ultime fiere ci sono domande chiare e dirette. Ora l’utente sa cosa vuole e ha solo bisogno di chiarirsi le idee sui costi e alcuni particolari della lavorazione.
Che livello tecnologico chiede il settore?
Chiede macchine affidabili e con costi di manutenzione bassi; accuratezza della superficie; precisione geometrica, fondamentale per i dettagli; possibilità di fare la fusione diretta, una sfida parzialmente vinta questa, in quanto ci sono le tecniche per fondere direttamente i nostri materiali, basta applicarle. Sicuramente, viviamo una corsa verso la qualità e la stabilità delle tecnologie. Importantissimo è il servizio, che per noi significa rispondere a una telefonata ed essere disponibili con il cliente, che magari in quel momento ha un dubbio. La semplicità d’uso è il tema che ci sta più a cuore: più le cose sono semplici, meno si rompono e meno problemi danno. Su questo aspetto la nostra ricerca è continua.
Che consigli date a chi si deve orientare nel settore?
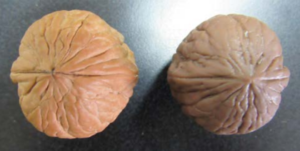